Your basket is currently empty!
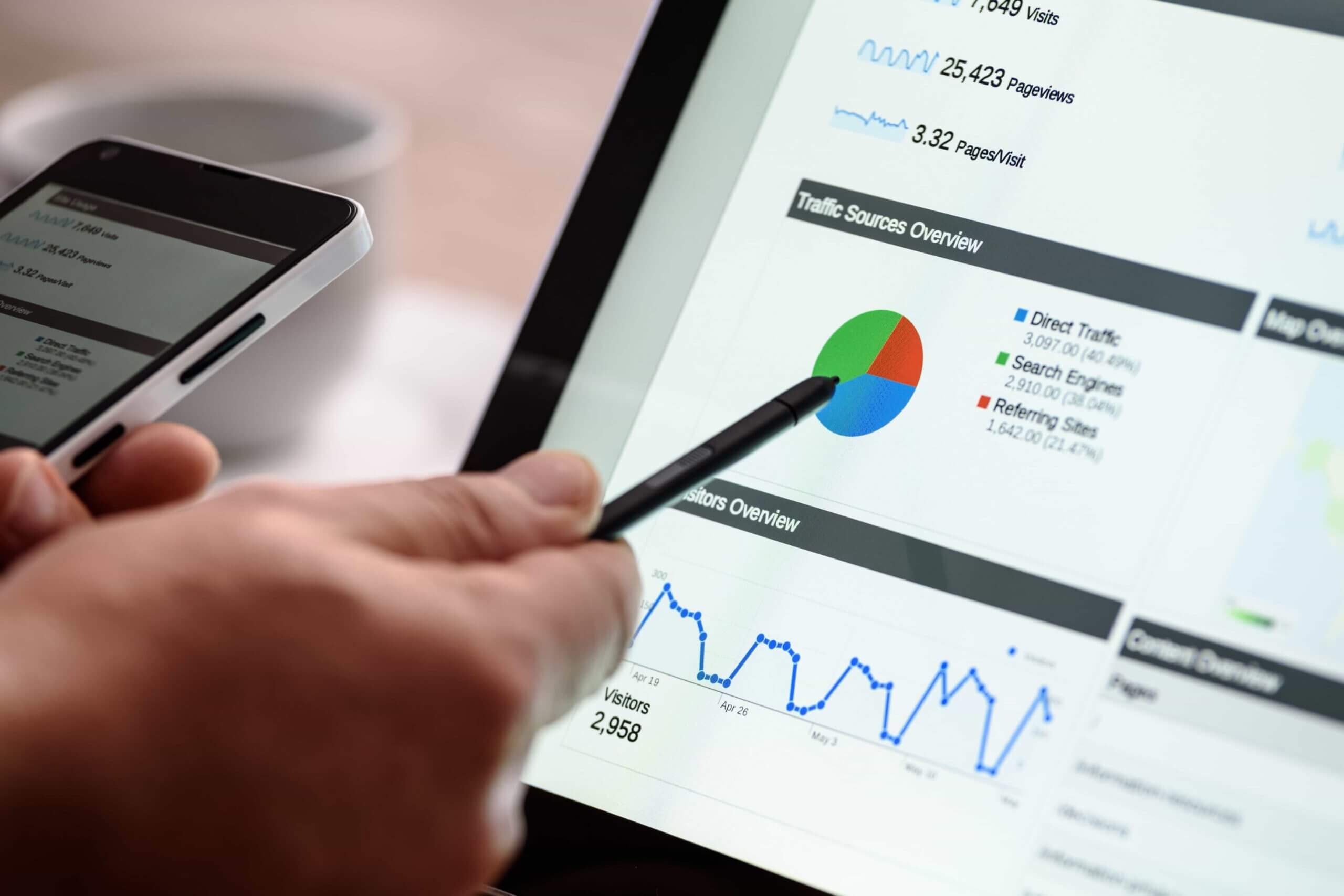
Cost planning is a crucial aspect of any construction project. It helps ensure that the project stays within budget while meeting its objectives. For UK-based construction businesses, understanding cost planning is vital for effective project management and financial control. In this blog, we will delve into the fundamentals of cost planning, offering insights from the Royal Institution of Chartered Surveyors (RICS) guidance, and explore how it supports project success.
What is Cost Planning?
Cost planning is the process of predicting, managing, and controlling the costs of a construction project from its inception to completion. It ensures that the client has a clear understanding of the likely costs and that the project is financially viable. It provides a framework to assess and monitor costs throughout the project life cycle.
The Role of Cost Planning in Construction Projects
For many businesses, particularly those new to construction or less familiar with the intricacies of financial management in this sector, cost planning can seem overly technical. However, it plays a vital role in the success of construction projects. By estimating and monitoring costs from the early design stages, businesses can avoid unforeseen expenses and cost overruns, which can jeopardize a projectโs profitability.
Cost planning works alongside the design and construction process, ensuring the client and the construction team remain aligned with the financial constraints. It ensures that the design is appropriate for the budget and identifies areas where value engineering can be applied to optimize the cost-to-benefit ratio without compromising the project’s quality or functionality.
Key Stages in the Cost Planning Process
The process of cost planning follows a structured approach aligned with RICS guidelines, often taking place over several stages as a project progresses:
1. Initial Cost Plan
The initial cost plan occurs during the early design stages of a project. Here, a quantity surveyor or cost consultant will develop a budget estimate based on broad parameters, such as project type, size, and complexity. At this stage, information may be limited, and the estimate is usually derived from historical data or benchmarks from similar projects. The New Rules of Measurement (NRM), specifically NRM1, is a useful tool in establishing order of cost estimates and managing this stage effectively.
2. Detailed Cost Plan
Once the design has progressed, a more detailed cost plan is developed. This plan involves breaking down the costs into more specific elements, such as structural work, mechanical and electrical systems, finishes, and external works. The cost consultant will work closely with designers to align the plan with the budget, identifying any areas where costs may exceed expectations and recommending value engineering strategies where necessary.
3. Cost Control During Construction
As the project moves into the construction phase, cost planning evolves into cost control. The budget must be monitored continually against actual expenditures. The use of interim valuations, cash flow forecasts, and change management systems ensures the project remains on track financially. If variations or unforeseen circumstances arise, adjustments to the plan may be necessary, but the goal is always to mitigate cost overruns as much as possible.
Benefits of Effective Cost Planning
Effective cost planning provides numerous benefits to construction businesses and their clients, including:
The Role of the Quantity Surveyor in Cost Planning
A quantity surveyor (QS) plays a pivotal role in cost planning. They bring technical knowledge, market insight, and cost expertise to the process, ensuring that budgets are realistic and achievable. The QS will prepare detailed cost estimates, monitor progress, and provide advice on cost-saving opportunities. Their involvement extends from the early feasibility studies through to final project completion, working closely with both clients and contractors to manage financial risks and ensure value for money.
RICS offers clear guidance on the role of the quantity surveyor in cost planning, emphasizing their responsibilities in providing accurate cost forecasts and ensuring accountability for project finances.
Key Tools and Methodologies in Cost Planning
To facilitate accurate cost planning, quantity surveyors use various tools and methodologies, including:
1. New Rules of Measurement (NRM)
The NRM provides a standard framework for measuring and reporting construction costs. It consists of three parts: NRM1 (order of cost estimates), NRM2 (detailed measurement for building works), and NRM3 (cost management for maintenance works). These rules enable consistent and transparent cost reporting across all stages of a project.
2. Benchmarking
Benchmarking involves comparing a projectโs costs against historical data from similar projects. This method helps in the early stages of cost planning when information may be limited, providing a basis for initial estimates.
3. Value Engineering
Value engineering is the process of reviewing the design and construction methods to identify cost-saving opportunities without compromising quality. This may involve selecting alternative materials, simplifying design features, or adjusting the construction sequence to reduce costs.
4. Cost Forecasting and Cash Flow Analysis
During the construction phase, cash flow forecasting helps to anticipate when funds will be required, ensuring that the project has sufficient liquidity at all times. This tool is essential for managing client expectations and avoiding cash flow shortages that could halt progress.
NRM1: The Foundation of Effective Cost Planning
The New Rules of Measurement (NRM1) is the standard set of guidelines provided by RICS for creating order of cost estimates and elemental cost plans. NRM1 offers a detailed framework for preparing early-stage estimates and forms the foundation of the cost planning process. This standardization ensures clarity and consistency, providing all stakeholders with a transparent breakdown of costs at each stage of a project.
NRM1 Elemental Cost Plan Template
The NRM1 breaks down the cost plan into key elements, each representing a portion of the building’s construction. Below is an example of how the NRM1 template is structured:
Element | Cost (ยฃ) | % of Total |
Substructure | ยฃ100,000 | 10% |
Superstructure | ยฃ250,000 | 25% |
Internal Finishes | ยฃ150,000 | 15% |
Mechanical & Electrical (M&E) | ยฃ200,000 | 20% |
External Works | ยฃ50,000 | 5% |
Preliminaries | ยฃ75,000 | 7.5% |
Overheads & Profit | ยฃ50,000 | 5% |
Risk Allowance | ยฃ50,000 | 5% |
Total Construction Cost | ยฃ925,000 | 100% |
This template organizes the project costs into individual elements of the building or site work. For a more accurate breakdown, NRM1 allows for each of these elements to be further subdivided into sub-elements, providing granularity in cost reporting and helping project teams identify cost-saving opportunities.
Project Program and Its Relationship to Cost Plan
The project program is closely linked to the cost plan because the timing of activities affects both cash flow and cost efficiency. A well-structured program ensures that costs are incurred as scheduled and that the project’s financial resources are allocated efficiently. Delays in the program can lead to increased costs, such as extended site management, prolonged equipment hire, and disruption of subcontractor schedules. For instance, if a project overruns due to design changes or poor coordination, costs can escalate, particularly in the preliminaries, which cover site setup, security, and temporary works.
Aligning the cost plan with the project program helps construction businesses anticipate financial requirements and adjust the plan in real-time to mitigate the risk of overruns. Quantity surveyors must regularly update both documents, ensuring that changes in the project schedule are reflected in the financial forecasts.
Project Location and Cost Implications
The location of a project plays a significant role in the cost plan. Factors such as local labour rates, availability of materials, and logistical challenges directly influence the project budget. For example, building in urban areas might incur higher costs due to restrictions on access, traffic management, and more expensive local services. Conversely, rural locations may require additional costs for transportation and site setup.
NRM1 provides flexibility to adjust the elemental cost plan to account for these variables. Location adjustments are typically made during the early cost estimation phase, where historical data and benchmarking against local projects can help set realistic expectations for the costs involved.
Risk Allowance in Cost Planning
The risk allowance is an essential component of the cost plan and is designed to cover unforeseen events that may impact the projectโs budget. This allowance accounts for the risks that have been identified but cannot be quantified precisely, such as bad weather, unexpected ground conditions, or regulatory changes. In NRM1, risk allowances are included as a specific line item to provide transparency and avoid underestimating the potential impact of project uncertainties.
Risk allowances are typically set as a percentage of the total project cost, depending on the complexity and size of the project. A robust risk management process helps in mitigating the likelihood of these risks materializing, but the risk allowance ensures that there is a financial buffer should unforeseen circumstances arise.
Why Do Project Costs Overrun?
Cost overruns are a common challenge in construction projects, often arising from several factors:
Cost planning, particularly with the use of NRM1, helps mitigate these risks by providing a detailed and structured approach to financial forecasting. Accurate early-stage planning, combined with regular updates and close monitoring of the cost plan, helps construction businesses stay on track and reduce the likelihood of cost overruns.
Overheads and Profit: How Are They Treated in Cost Planning?
In cost planning, overheads refer to the indirect costs of running a construction project, which are not directly tied to specific activities or materials. This can include office expenses, insurance, project management fees, and administrative costs. Profit represents the contractorโs financial return on the project.
Under NRM1, overheads and profit are typically included as separate elements within the cost plan, ensuring transparency for the client. These are usually calculated as a percentage of the total construction cost, with typical ranges for overheads being 5-10%, depending on the nature of the project and the contractorโs internal costs. Profit margins can vary widely, generally ranging between 5-20%, depending on market conditions and the competitive landscape.
Conclusion
Cost planning is not just about keeping projects within budget; itโs a critical tool for ensuring project success. By understanding the various elements, such as the NRM1 cost plan template, project program alignment, risk allowances, and the impact of location, businesses can make more informed decisions. Additionally, recognizing the reasons for cost overruns and how overheads and profit are integrated into the cost plan helps construction businesses safeguard against financial risks.
Assignment Bill of Quantities Bonds breach Building Contracts Collateral Warranties Construction Act 2009 Consultancy contract contract practice Contracts Contracts (Rights of Third Parties) Act 2009 Cost Plan CW damages Disputes Economic Development and Construction Act 2009 Equitable Assignment FIDIC Force Major Insurance JCT LDEDCA Legal Assignment Letter of Intent LOI NEC NRM Obligations oral Parent Company Guarentee Payless Payment PCG provision Provisions Retention statutory Suspension terms Third Party Rights tort uk Understanding the Local Democracy Warranty